
Contents
Quality Policy
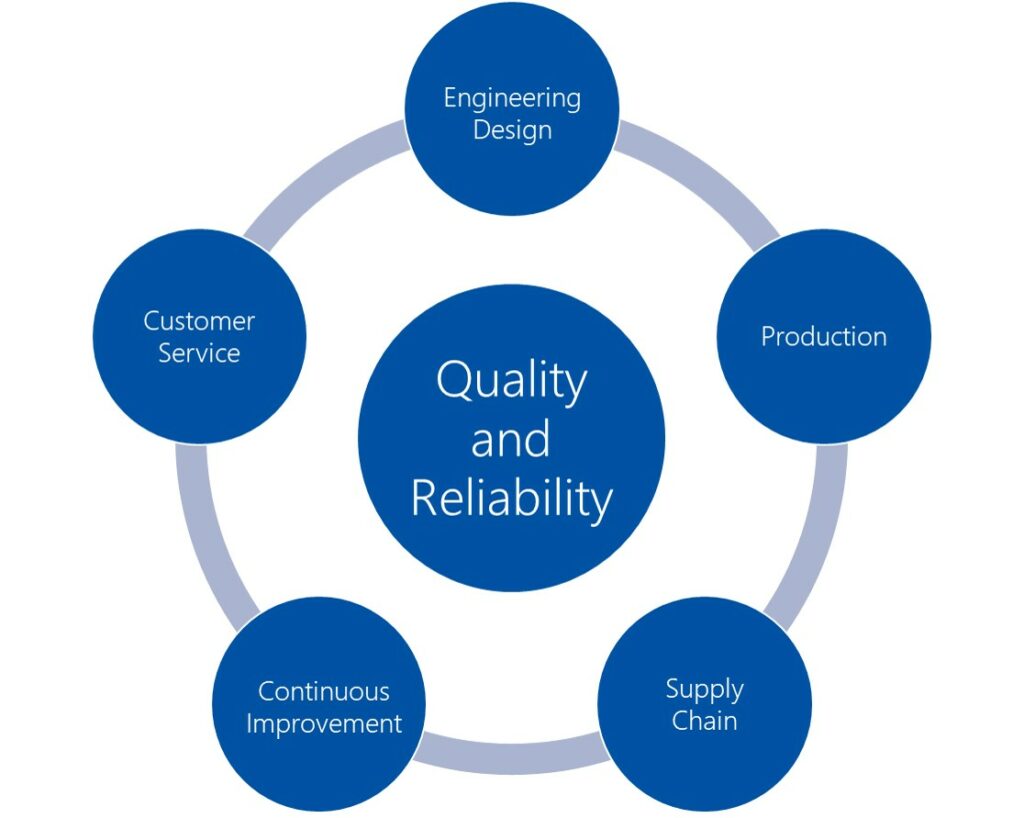
- At CTS, we must meet the company value, think for the customer, and consider the impact on the environment.
- All staff, suppliers and vendors shall implement customer-driven quality management system to achieve and maintain the highest quality standards.
- CTS will strive to reach our ultimate goal by building an effective quality assurance system, continuously improving services, and managing Environmental, Safety, and Health (ESH) risks.
TOP
Organization of QA
We see quality and reliability as the credibility of CTS. We manage quality systems, promote design quality, ensure manufacturing quality, and support customers with a cross-functional team.
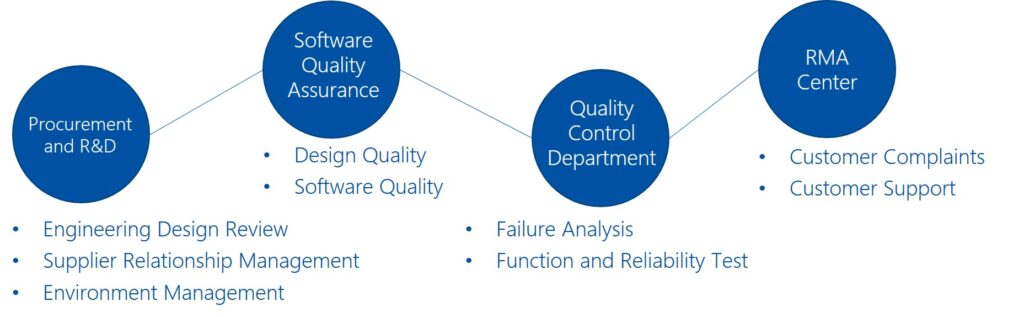
TOP
Engineering Design
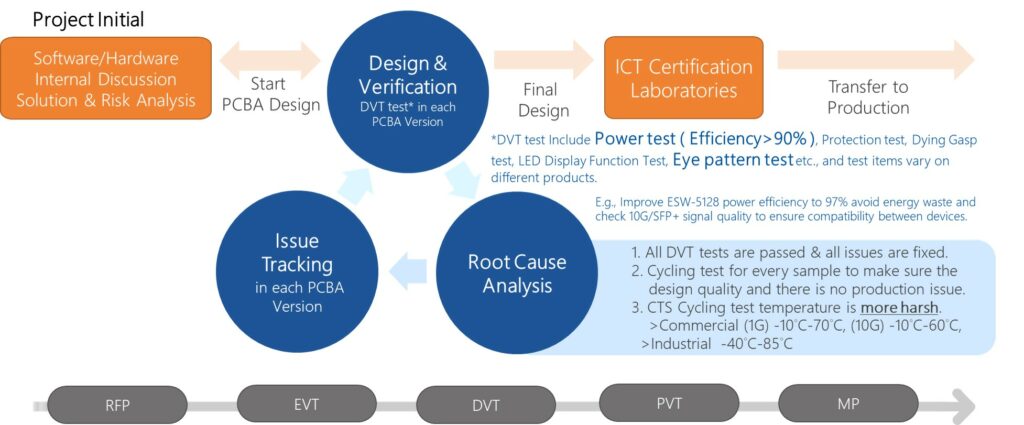
Supplier Relationship Management
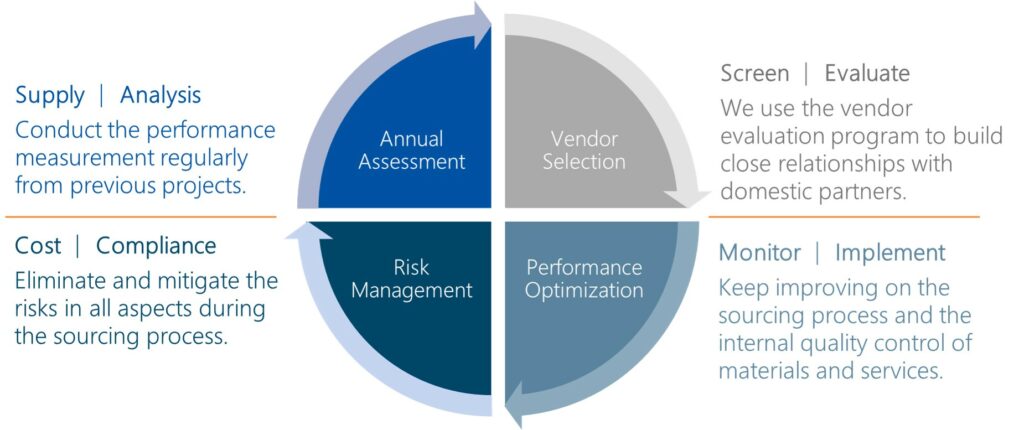
TOP
Environmental Management
Product Design
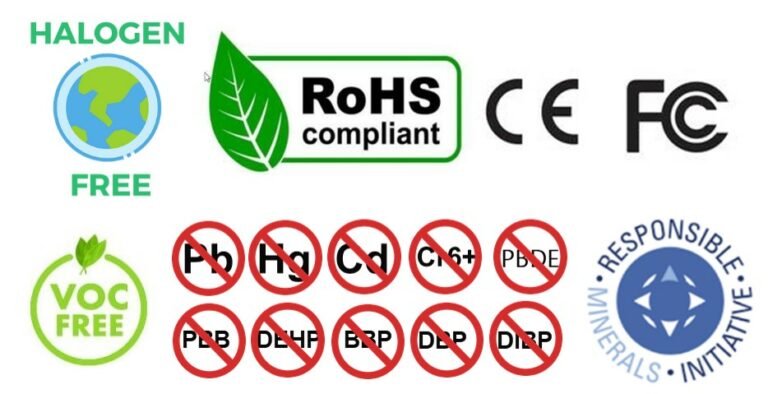
Reducing Packaging Material
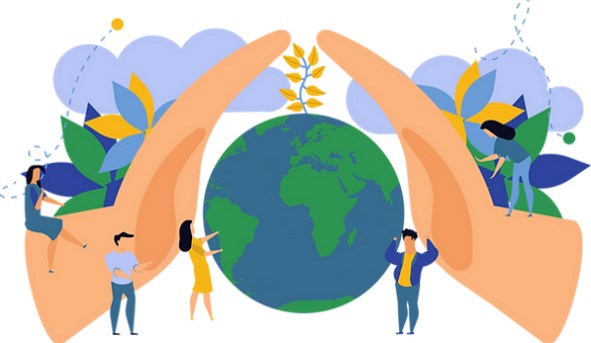
Software Quality Assurance
Requirement Analysis (New Products, New Features)
Test Planning and Design
Test Execution
Retesting
Release Testing Result for Internal Discussion
Full Function Test (UI, Protocol…)
- Test coverage of all core functions is close to or equals 100%
Partial Test (All Functions Related)
- Existing functionality was not affected by the changes
- System performance corresponds to the requirements
Verification Test (Specific Feature)
- Extensive testing will be integrated into each development phase
Sample Test (Before Mass Production)
TOP
Manufacturing Quality
Dynamic Burn-in Room
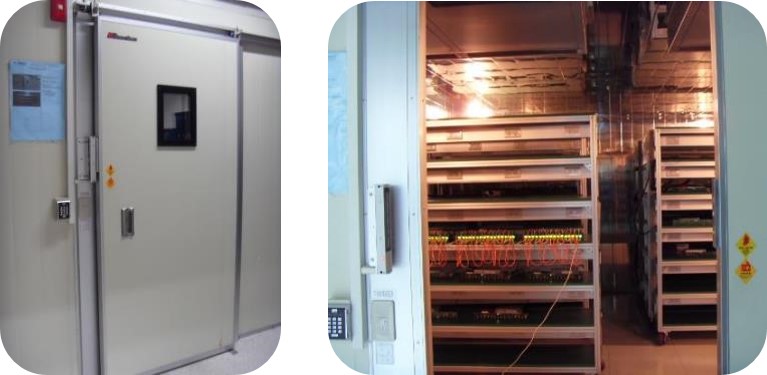
ALL the products
are being tested for 8 hours,
with operating temperature 50°C,
before shipping out to customers.
First pass yield (%)= Quality units / Total units
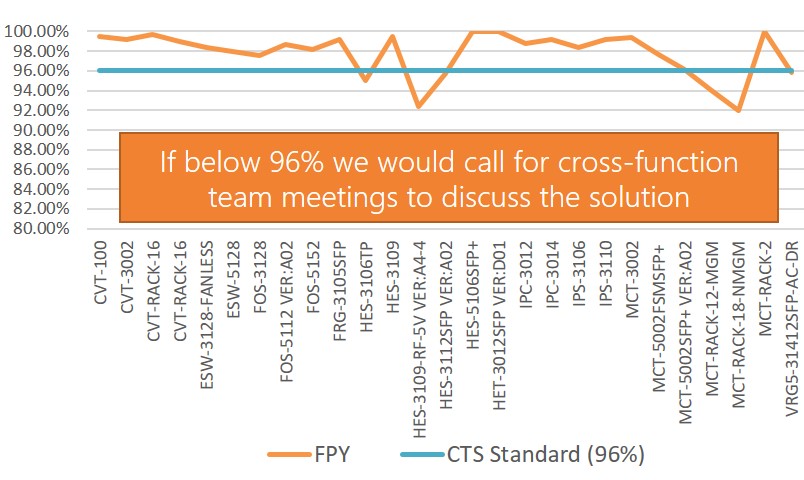
We record the first pass yield to make sure
that our design have the right quality,
can reduce waste and improve workflow.
Reliability Test
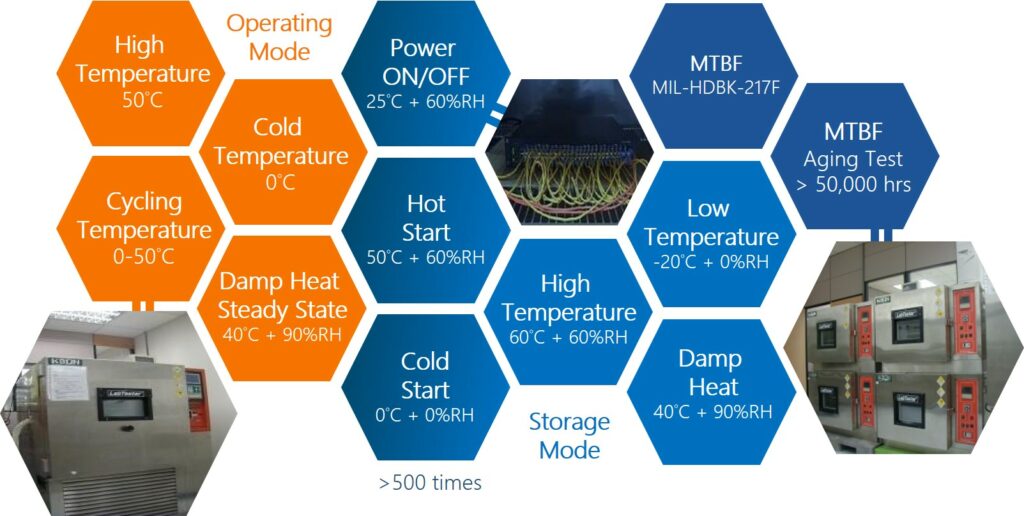
Failure Analysis
- We calculate MTBF with International Standard MIL-HDBK-217F with 25℃ and 40 ℃. (Active and passive components are being calculated.)
- We also do the Accelerated Aging Test (6+ months) to collect the real life data of our products.
WHY
- We use higher temperatures to accelerate the aging process by representing Real-Time Aging artificially.
- It helps us identify issues accurately, and get products to market with less risk.
- We gain customer trust and confidence
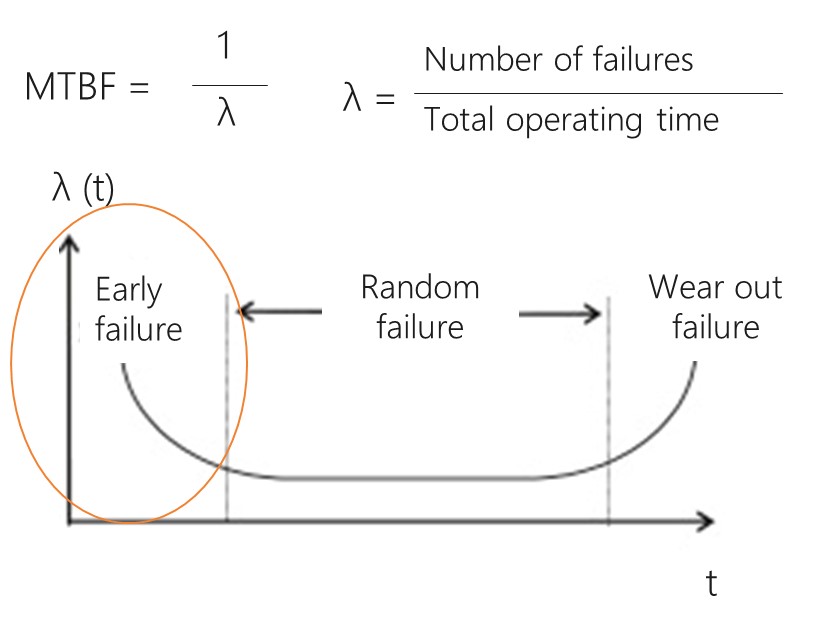
Traceability
Manufacturing history can be traced if there’s any quality issue. Main traceable details include: Manufacturing history, Testing results, Final Quality Control, Outgoing Quality Control, Shipping Record, etc.
◆ Serial Number Example
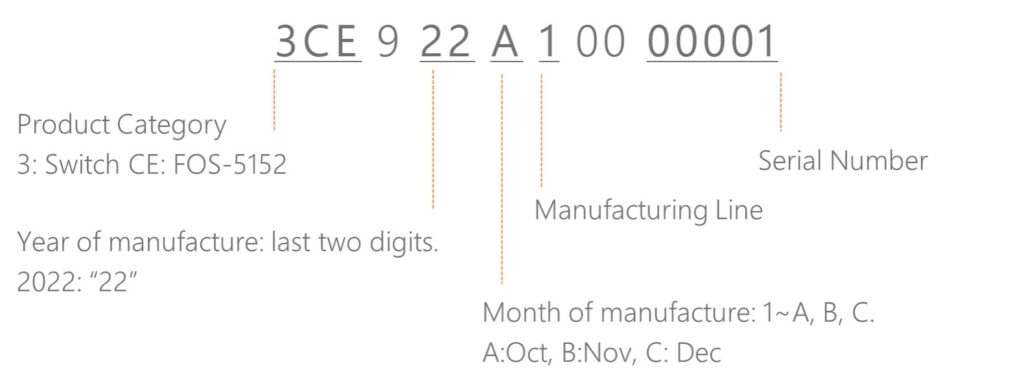
Customer Support
If there’s any issue or defects found by the customers, our team will provide support to identify the cause, thoroughly analyze, and take counter-measures to prevent recurrence of the defect.
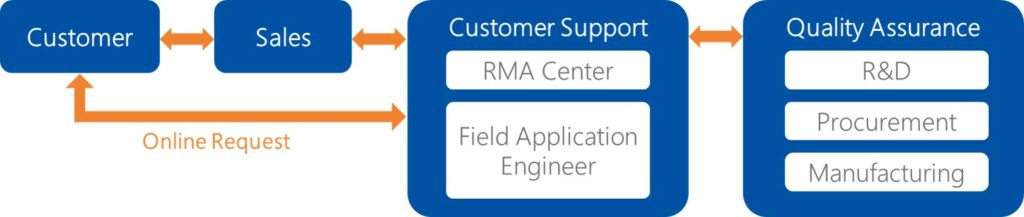
CTS always puts effort on our analysis data and uses it as the guide to improve our quality assurance system.
TOP
ISO Certification
Quality management system (QMS)
ISO 9001
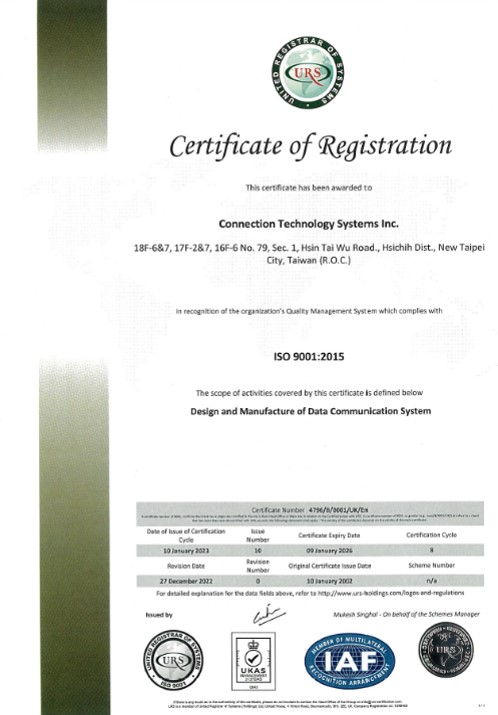
Environmental management system (EMS)
ISO 14001
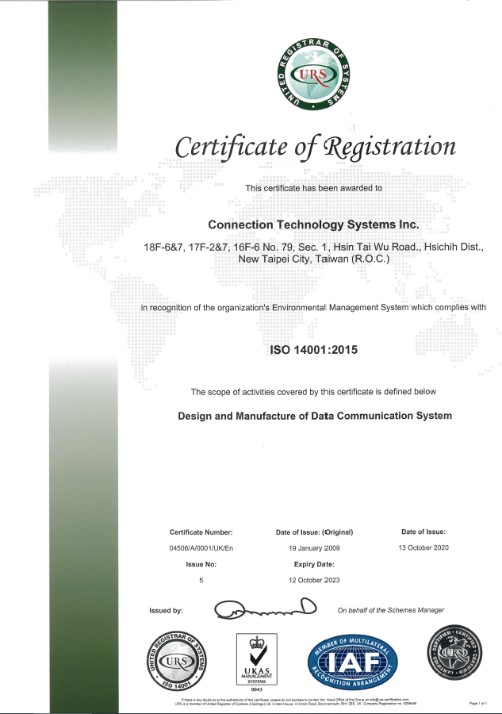
TOP
CTS Quality
To conclude, CTS seeks to deliver the best quality, service, and performance in order to provide the customers with the benefits beyond the visible costs.
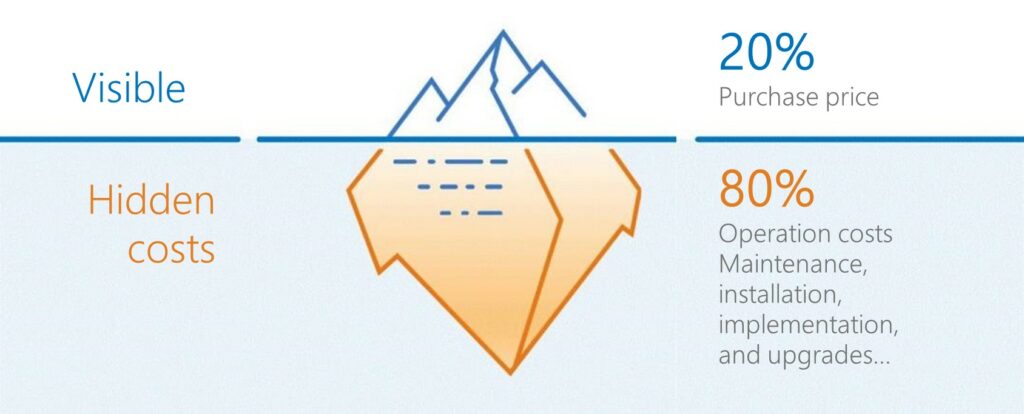
Quality Policy
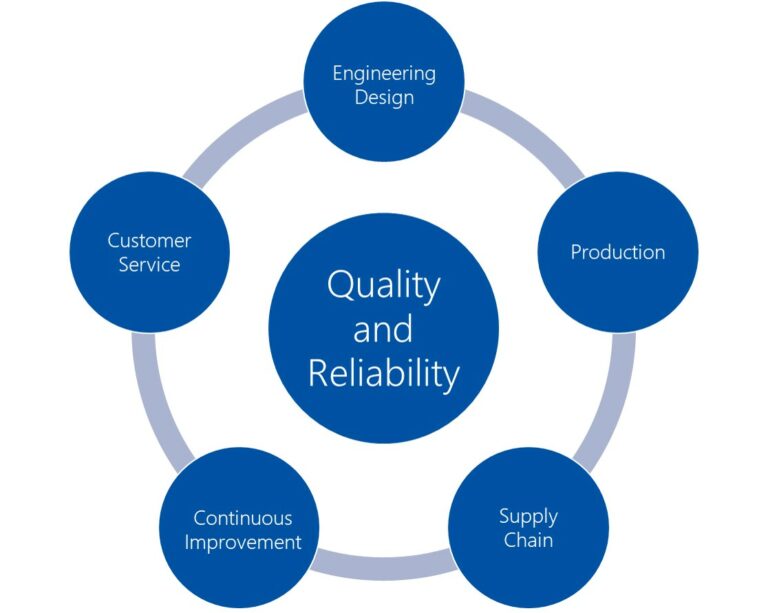
- At CTS, we must meet the company value, think for the customer, and consider the impact on the environment.
- All staff, suppliers and vendors shall implement customer-driven quality management system to achieve and maintain the highest quality standards.
- CTS will strive to reach our ultimate goal by building an effective quality assurance system, continuously improving services, and managing Environmental, Safety, and Health (ESH) risks.
TOP